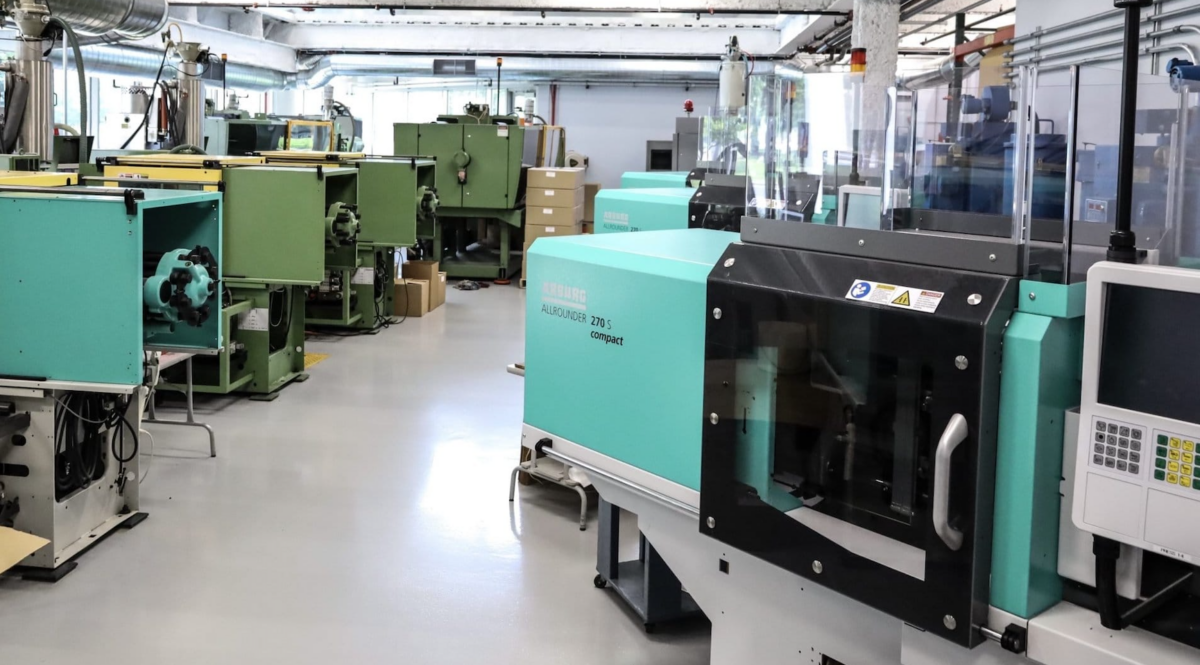
Big Picture: Ultrasonic Welding
Ultrasonic welding is a fast, clean, and reliable method for bonding plastics without adhesives or fasteners. It relies on high-frequency vibrations to create a solid-state weld – an essential process in industries requiring precision and efficiency.
As 2025 progresses, innovations in ultrasonic welding continue to push manufacturing forward, improving bond strength, production speed, and overall efficiency.
If you are looking for a reliable Plastic Injection Molding Company to partner with, JDI Plastics consistently achieves top-quality plastic products and components across many industries. Our advanced capabilities include ultrasonic welding and much more.
Reach out to JDI Plastics today and experience the benefits of working with an experienced injection molding company.
Table of Contents
What is Ultrasonic Welding?
Ultrasonic welding is a technique that uses high-frequency acoustic vibrations to fuse plastics together under pressure.
Unlike traditional welding, it doesn’t rely on external heat, adhesives, or solvents.
Instead, friction from ultrasonic energy creates a focused, localized melt, forming a durable bond in seconds.
Key Features of Ultrasonic Welding:
- Rapid processing times
- No need for adhesives or solvents
- Low energy consumption
- Ability to join dissimilar materials
- Minimal thermal impact on components
How Does Ultrasonic Welding Work?
Ultrasonic welding converts electrical energy into mechanical vibrations, which are applied to the plastic components being joined.
These vibrations create friction at the interface, generating heat that softens and fuses the materials without reaching their melting point.
Ultrasonic Welding Process Components
Component | Description |
---|---|
Power Supply | Generates high-frequency electrical energy. |
Converter | Transforms electrical energy into mechanical vibrations. |
Booster | Adjusts the amplitude of vibrations. |
Sonotrode (Horn) | Directs vibrations to the materials being welded. |
Anvil/Fixture | Provides support for the materials during welding. |
Applications of Ultrasonic Welding in Plastic Manufacturing
Ultrasonic welding plays a key role in several industries – thanks to its ability to create precise, strong, and contamination-free bonds.
Automotive Industry
Automotive manufacturers use ultrasonic welding to assemble interior and exterior plastic components, such as instrument panels, door panels, and air filters. The process creates seamless, durable joints without adding unnecessary weight – ideal for modern vehicle production.
Medical Industry
Medical device manufacturers rely on ultrasonic welding to assemble sterile products like IV catheters, surgical instruments, and face masks. Since the process doesn’t introduce adhesives or excessive heat, it maintains the integrity of sensitive medical components.
Electronics Industry
In electronics, ultrasonic welding is commonly used for circuit boards, wiring harnesses, and microelectronic components.
This process is essential for small and delicate parts because it provides a secure connection without the risk of heat damage.
Advantages of Ultrasonic Welding
Ultrasonic welding has become a go-to solution in manufacturing. The process is clean, energy-efficient, and scalable for high-volume production.
Manufacturers prefer ultrasonic welding for its ability to create strong, precise welds while cutting down on material waste and production time.
Benefits Include:
- Fast processing speeds – Reduces cycle times and increases output.
- Strong, clean joints – No need for additional bonding agents or chemicals.
- Energy-efficient process – Uses less power compared to traditional welding methods.
- Automation-friendly – Works seamlessly with robotics for consistent results.
- Minimal heat exposure – Protects sensitive components from thermal damage.
Challenges and Considerations in Ultrasonic Welding
Ultrasonic welding is highly effective, but it comes with some considerations.
Material compatibility is a big factor—certain plastics don’t respond well to ultrasonic vibrations, and part design must accommodate this.
Features like energy directors, joint geometry and wall thickness impact weld quality. Careful planning is required for a strong, reliable bond.
Another challenge is the upfront cost of ultrasonic welding equipment. While it significantly reduces long-term operating expenses, the initial investment can be substantial. Training operators on proper settings and techniques is also essential to avoid weak welds or defects.
Despite these challenges, manufacturers find that the benefits far outweigh the challenges when the process is correctly implemented.
Recent Advancements in Ultrasonic Welding Technology
As of 2025, ultrasonic welding continues to evolve with new technology that improves precision, efficiency, and ease of use. Modern systems offer greater control over the welding process.
Notable Advancements:
- Fully electric ultrasonic welding systems – Servo motors provide more precise control over parameters.
- User-friendly interfaces – Reduce setup time and simplify operation.
- Enhanced energy efficiency – Supports sustainable manufacturing practices.
- Improved weld monitoring – Advanced sensors and software track weld quality in real time.
How Strong is Ultrasonic Welding?
Ultrasonic weld strength depends on multiple factors: The materials used, joint design, and process settings.
In most cases, ultrasonic welds are as strong as or stronger than the base materials.
Factors Influencing Weld Strength
Factor | Impact on Strength |
---|---|
Material Selection | Affects molecular bonding and weld durability. |
Energy Director/Joint Design | Ensures even distribution of ultrasonic energy. |
Process Parameters | Proper settings for pressure, time, and amplitude improve weld integrity. |
JDI Plastics | Injection Molding You Can Rely On
From automotive components to medical devices, ultrasonic welding’s ability to create strong, clean bonds without adhesives makes it a valuable capability for Injection Molding manufacturing.
If you are ready to optimize your operation with a reliable injection molding company, contact JDI Plastics today!
Visit our homepage HERE.
Reference:
(1) Ultrasonic Welding, Science Direct, https://www.sciencedirect.com/topics/engineering/ultrasonic-welding