Plastic Product Development: Injection Molding
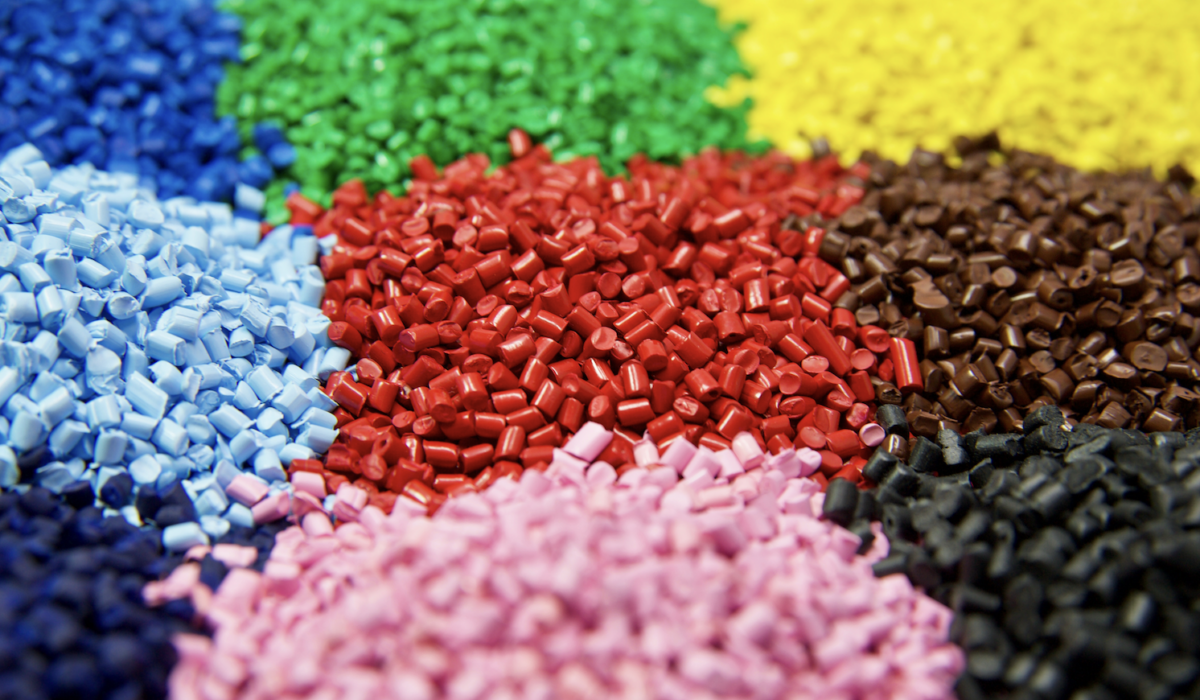
Table of Contents
Intro: Plastic Product Development
Plastic product development involves designing, prototyping, and manufacturing high-quality plastic parts using processes like injection molding to meet specific application needs.
Injection molding is one of the most common methods of plastic part manufacturing. Injecting molten plastic in customized molds is a reliable, cost-efficient, and capable method of forming tailored plastic components.
This article from JDI Plastics discusses the methods of developing plastic products with an injection molding company – from early supplier involvement to market production. We are an injection molding company devoted to providing the highest quality experience for our clients.
With JDI Plastics, plastic product development is tailored to refine your concept into a streamlined, finished product.
Key Takeaways
- Injection molding produces complex plastic parts at scale.
- Strong materials like ABS, Nylon, and PC provide durability and flexibility.
- Prototyping minimizes costs and optimizes design.
- Industries like automotive manufacturing and construction rely heavily on injection molding.
- Close collaboration between design and production teams enhances performance.
Key Insights on Plastic Product Development
Aspect | Details | Examples |
---|---|---|
Primary Industries | Automotive, construction, medical, consumer goods | Dashboards, piping, medical devices |
Common Materials | ABS, Nylon, PVC, Polycarbonate | Lightweight, durable components |
Prototyping Methods | 3D Printing, CNC Machining, prototype molding | Cost-effective design testing |
Injection Molding Benefits | Scalable production, high precision, repeatable quality | Mass production of complex parts |
Development Steps | Concept design, material selection, prototyping, tooling, and production | End-to-end manufacturing solutions |
Future Trends | Bio-based plastics, energy-efficient molding, advanced prototyping technologies | Sustainable and innovative designs |
What Is Plastic Product Development?
The Role of Prototyping
Prototyping improves part functionality and manufacturability by allowing designers to identify and correct potential issues early. It’s pretty much essential for a cost-optimized operation.
Rapid prototyping methods, such as 3D printing, CNC machining, and prototype molding, offer fast and cost-effective ways to create accurate prototypes before committing to production molds.
Material Selection for Injection Molding
Choosing the right material is critical for the success of a plastic product.
Factors like strength, flexibility, thermal stability, and cost all play a role. Materials like ABS offer impact resistance and durability, while PC provides optical clarity and strength. Nylon is a popular choice for wear-resistant components.
The selected material must align with the product’s performance requirements and operating environment.
Benefits of Injection Molding in Product Development
Injection molding is one of the most versatile and efficient methods for creating high-quality plastic parts. Its ability to produce complex geometries with high precision makes it essential for industries requiring intricate and reliable designs. Manufacturers can produce parts with consistent dimensions and minimal defects, even in high-volume production.
The repeatability of injection molding is a major advantage.
Once a mold is created, it can produce thousands or millions of identical parts – ideal for mass production while maintaining tight tolerances. The inherent reduction in variability risk ensures that every component meets exact specifications.
Sustainability is another key benefit.
Injection molding minimizes material waste, as excess plastic can often be reground and reused. It also supports the use of recycled plastics. Injection molding continues to align with modern sustainability goals with advancements in bioplastics and energy-efficient machinery.
Applications of Plastic Product Development
Automotive Industry
Injection molding is responsible for the production of lightweight yet durable components in modern vehicles. The advanced capabilities of injection molding companies have allowed automotive manufacturers to design much lighter-weight vehicles.
Plastics like ABS and nylon create dashboards, bumpers, housings, and interior trim. These materials reduce overall vehicle weight to enhance fuel efficiency while maintaining strength and durability.
Precision molding also supports intricate designs for complex parts that meet the high standards of the automotive industry.
Construction Industry
Molded plastics play a significant role in construction due to their versatility and cost-effectiveness.
Materials like PVC and HDPE are used in piping systems, insulation, and structural components. These plastics are ideal for long-term applications because they offer excellent resistance to wear, weather, and chemicals.
Their lightweight nature also simplifies installation, which saves time and labor costs on construction sites.
The Process of Plastic Product Development
Key Steps in Development
Plastic product development follows a structured process that transforms concepts into functional parts:
- Concept Design: Outlines the product’s purpose, dimensions, and specifications.
- Material Selection: Chooses plastics based on application needs like strength, flexibility, and thermal resistance.
- Prototyping: Creates a prototype to test and refine the design before production.
- Tooling and Mold Creation: Builds precise molds for mass production, ensuring high-quality, repeatable results.
FAQs: Plastic Product Development
What is an example of development in plastic?
A common example is prototyping and designing injection-molded parts for automotive components like housings and electronic connectors.
What is the process of plastic production?
Plastic production involves design, prototyping, molding, and finishing to create functional parts.
What is the basic concept of plastic product design?
The basic concept focuses on balancing functionality, aesthetics, and manufacturability to meet specific application needs.
What is the future of plastic production?
The future includes advancements like bio-based plastics and energy-efficient molding technologies.
JDI Plastics: Why Plastic Product Development Matters
Plastic product development is at the very heart of modern manufacturing. It enables precise, cost-effective production across industries. From automotive to construction to medical instruments, injection molding supports innovation with lightweight, durable, and versatile plastic components.
JDI Plastics is a trusted partner for comprehensive plastic product development. With expertise in prototyping, material selection, and injection molding, we deliver high-quality solutions tailored to meet your needs.
Call JDI Plastics today for your Injection Molding needs!
Reference:
(1) What is Product Development, IBM, https://www.ibm.com/think/topics/product-development