Plastic Injection Molding for Electronics – High-Performance Solutions for Illinois Consumer Electronics
Why Plastic Injection Molding is Ideal for Consumer Electronics
Illinois-based Injection Molding Company JDI Plastics delivers precise and durable injection molding solutions specifically designed for the consumer electronics industry, producing high-quality components that meet the stringent demands of modern devices.
Plastic injection molding is a perfect fit for consumer electronics because it combines durability, cost-efficiency, and precision. The process allows manufacturers to produce complex parts at high volumes, with accuracy and consistency being key benefits.
Injection molding can scale to meet the needs of any electronics manufacturer for premium structural elements, intricate functional components, and virtually everything else made of plastic.
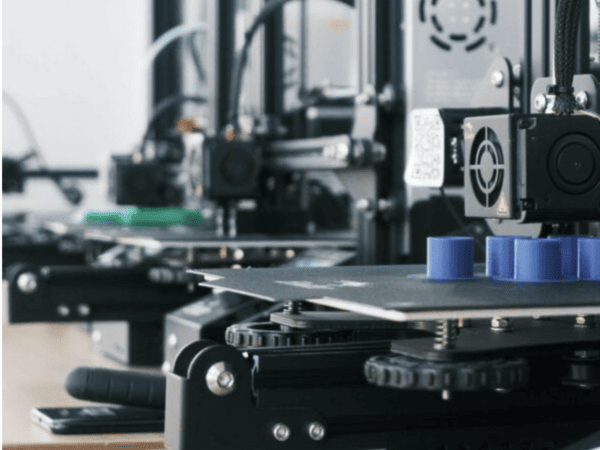
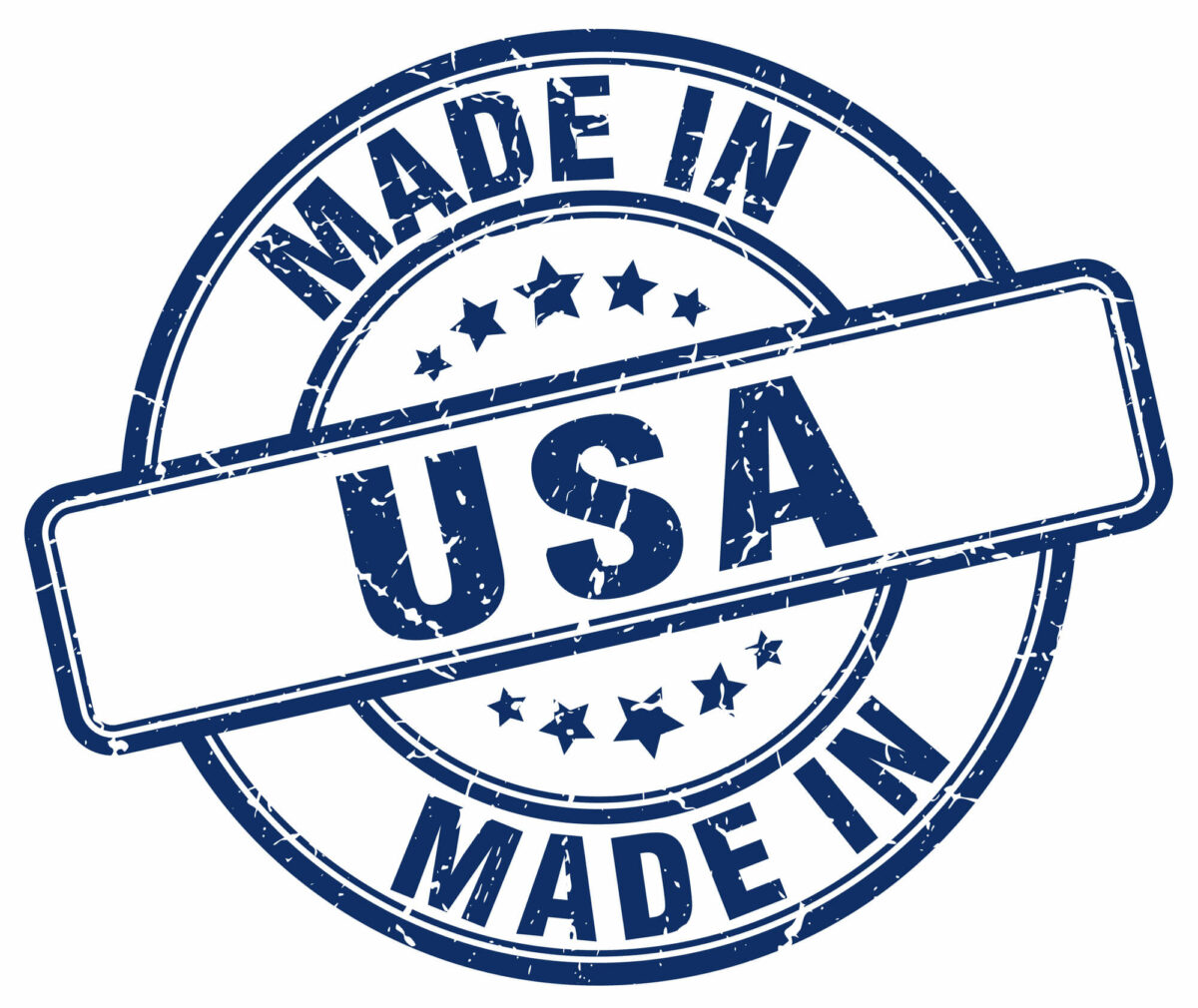
The JDI Advantage
Material versatility: A wide range of plastics can be used for specific applications.
Design flexibility: Complex shapes and parts are easily manufactured.
Cost-effectiveness: Efficient production at lower costs.
Scalability: High-volume production with consistent quality.
High-tolerance production: Ensures exact dimensions for critical parts.
High-Volume Production | Allows for efficient, large-scale production, reducing lead times and lowering costs. |
Design Flexibility | Enables the creation of complex and intricate parts, essential for modern electronic devices. |
Material Versatility | Supports a wide range of materials, including Polycarbonate, ABS, and Nylon, to meet different product needs. |
Precision and Accuracy | Produces high-tolerance parts critical for fitting complex internal components in electronics. |
Durability | Ensures parts like connectors, housings, and circuit supports are durable for long-term use. |
Cost-Efficiency | Reduces material waste and overall production costs, especially in high-volume runs. |
Customization Options | Provides the ability to create custom molds, allowing for brand-specific designs and unique features. |
Consistency | Delivers repeatable quality, ensuring every part meets exact specifications, ideal for mass production. |
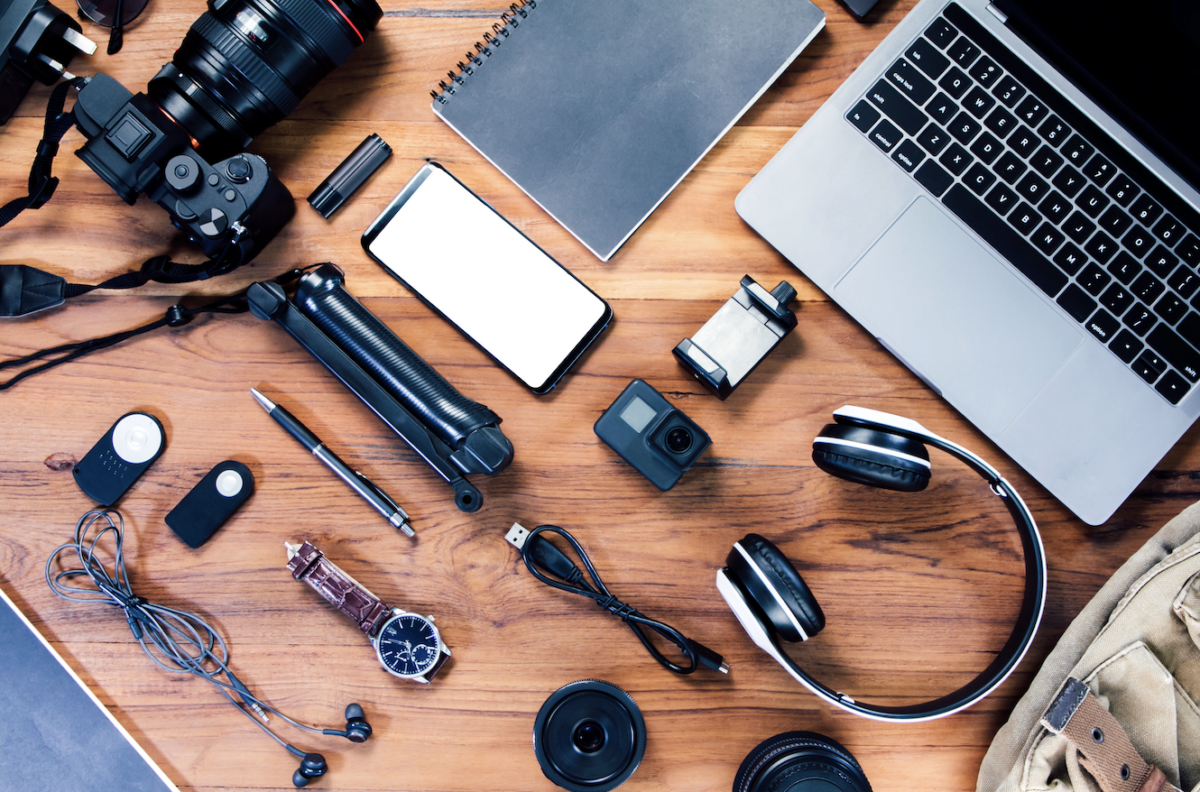
Electronics Components Produced with Plastic Injection Molding
Injection molding is essential for creating both structural and functional parts in electronics.
From housings that protect delicate components to internal parts that provide connectivity and function, injection molding provides reliable, scalable solutions. The precision involved makes it ideal for electronics where components must fit perfectly to ensure proper function and durability.
Many consumer electronics parts are produced this way. Injection molding allows manufacturers to meet demand while maintaining quality.
Examples:
- Device housings: Protects internal components from damage.
- Circuit board supports: Stabilizes the mainboard within devices.
- Connectors: Ensures secure, reliable, and safe electrical connections.
- Battery enclosures: Provides safety and longevity for battery units.
- Cable insulators: Protects electrical wiring and ensures safe connections.
- Keypads and buttons: Provides durable, responsive user interfaces.
- Speaker components: Helps in housing and stabilizing internal speaker mechanisms.
- LED light diffusers: Distributes light evenly and prevents glare in electronic displays.
Materials Used in Plastic Injection Molding for Electronics
Materials used for electronics must combine properties like thermal resistance, electrical insulation, and mechanical strength to handle the unique demands of consumer products.
Injection molding allows for the use of materials that meet these needs. It provides unmatched flexibility to create durable, high-performance components.
Common Materials:
- Polycarbonate: Strong, durable, and used for housings and lenses.
- ABS: Commonly used for structural parts with impact resistance.
- Nylon: Ideal for connectors and parts requiring flexibility.
- PEEK: Great for high-temperature and demanding environments.
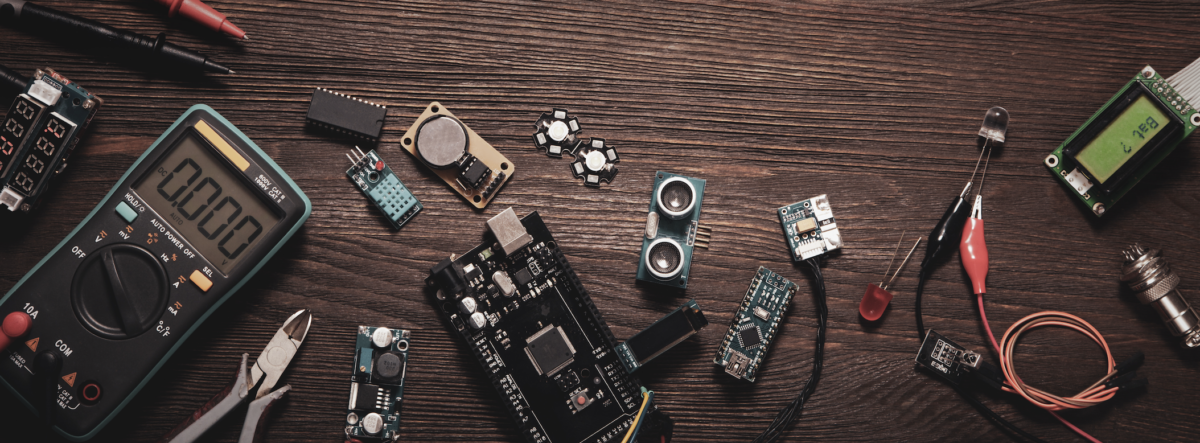
Benefits of Injection Molding for Illinois Electronics Manufacturers
Injection molding provides numerous benefits to electronics manufacturers in both our home of Illinois and across the Country.
The process increases production efficiency by enabling large-scale production of high-quality components with consistent precision. It also offers customization options to easily create intricate designs and tailor parts for specific needs.
- Reduced production time for faster time-to-market.
- Waste minimization leading to lower costs.
- Consistent quality across high-volume production.
- Ease of mass production with precise, repeatable results.
Frequently Asked Questions About Injection Molding for Electronics
How does injection molding enhance the quality of electronic devices?
Injection molding allows for precise, repeatable manufacturing that produces components such as housings and connectors that fit perfectly and perform reliably. This results in consistent quality for mass-produced electronic devices.
Can injection molding be used for both small and large electronic components?
Yes, injection molding is versatile and can be used to produce both small, intricate parts like micro-connectors as well as larger items like device casings.
What role does injection molding play in improving product sustainability?
Injection molding can reduce material waste and allow for the use of recyclable plastics to reduce the footprint of each component produced.
JDI Plastics: A Reliable Partner for Plastic Injection Molding in Electronics
JDI Plastics brings years of experience in producing high-quality plastic components for the consumer electronics industry. Our injection molding services are designed to deliver durable, precision-made parts that meet the exacting standards of electronics manufacturers.
By choosing JDI, you benefit from our expertise in custom tooling, use of advanced technologies, and commitment to delivering reliable solutions that help you achieve production goals efficiently.
With early supplier involvement and a commitment to quality, JDI Plastics will always stove to exceed your expectations!
Reach out with questions today!
Markets Served
We tailor our services and requirements around the needs of each individual customer, which allows us to provide the best performance at a very competitive price. We are proud to be able to offer our customers more solutions so that they can narrow down their supply chain and supplier base.