Medical Injection Molding in Illinois – Trusted by Medical Manufacturers
Why Choose JDI Plastics for Medical Injection Molding in Illinois?
At JDI Plastics, we provide high-quality, FDA-compliant medical injection molding services that Illinois medical manufacturers trust for precision, reliability, and cost-efficiency.
We understand the importance of delivering medical-grade products that meet the highest standards. From concept to completion, we’re committed to providing our Illinois-based medical manufacturers with components that are consistent, reliable, and designed to perform.
Our team works closely with clients to ensure every part meets the specific demands of the healthcare industry.
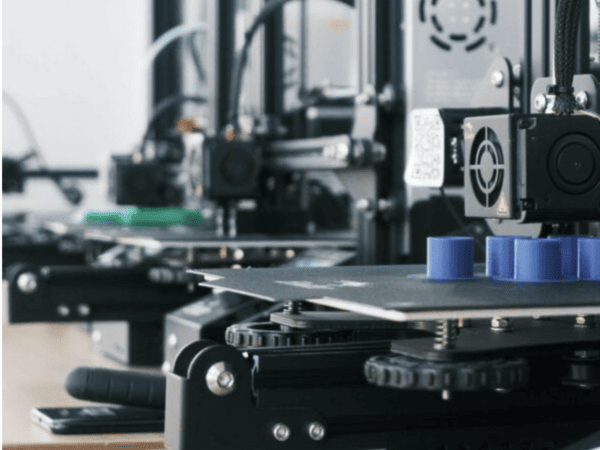
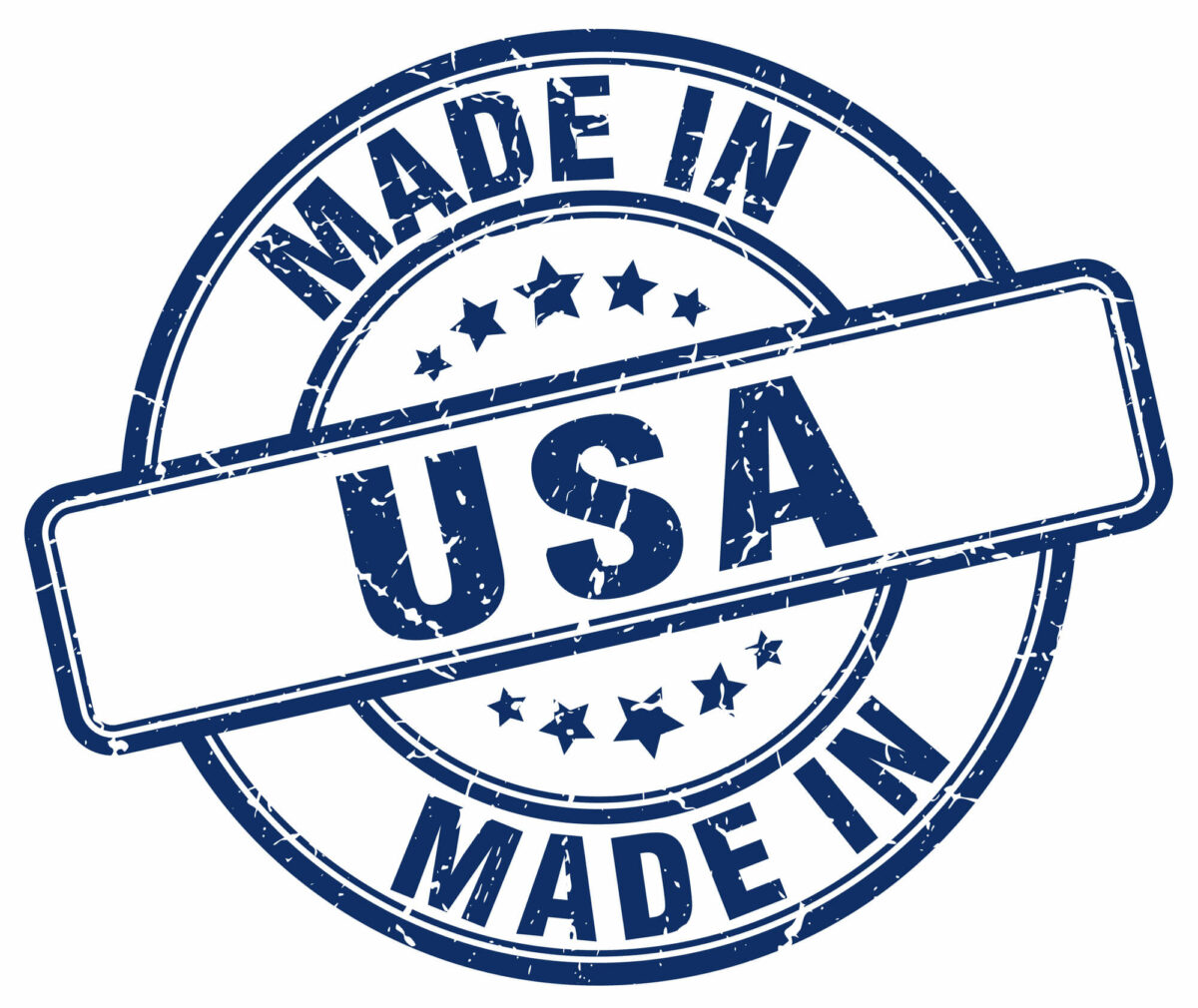
The JDI Advantage
Cost-efficient solutions that don’t compromise on quality.
Rapid turnaround times thanks to streamlined processes and local support.
Regulatory compliance with FDA-approved materials and processes.
Custom designs are tailored to meet the exact specifications of your medical device.
Exceptional customer service every step of the way.
FDA Compliance | All materials and processes used should be FDA-approved to ensure safety and regulatory compliance. |
Material Options | Thermoplastics, elastomers, and biocompatible polymers are the most common materials used. |
Precision & Accuracy | High-tolerance molding ensures that intricate medical devices, like surgical tools, are produced with exact specifications. |
Customization Capabilities | Custom tooling and mold designs allow manufacturers to create unique parts that meet their specific needs. |
Scalability | Injection molding is ideal for high-volume production, capable of producing hundreds of thousands of parts consistently. |
Sterilization Requirements | Molding companies should offer sterilization-ready processes and materials to produce clean, safe medical devices. |
Turnaround Time | Fast production cycles reduce lead times, allowing medical manufacturers to bring products to market quickly. |
Cost-Efficiency | Injection molding provides cost-effective solutions for mass production, minimizing waste and reducing material costs. |
Durability & Lifespan of Molds | High-quality molds can last through thousands of production cycles, ensuring long-term cost savings for manufacturers. |
Secondary Services | Assembly, packaging, and post-production services streamline the manufacturing process for medical device companies. |
Regulatory Knowledge | A reliable injection molding partner understands and complies with healthcare-specific regulations such as ISO 13485. |
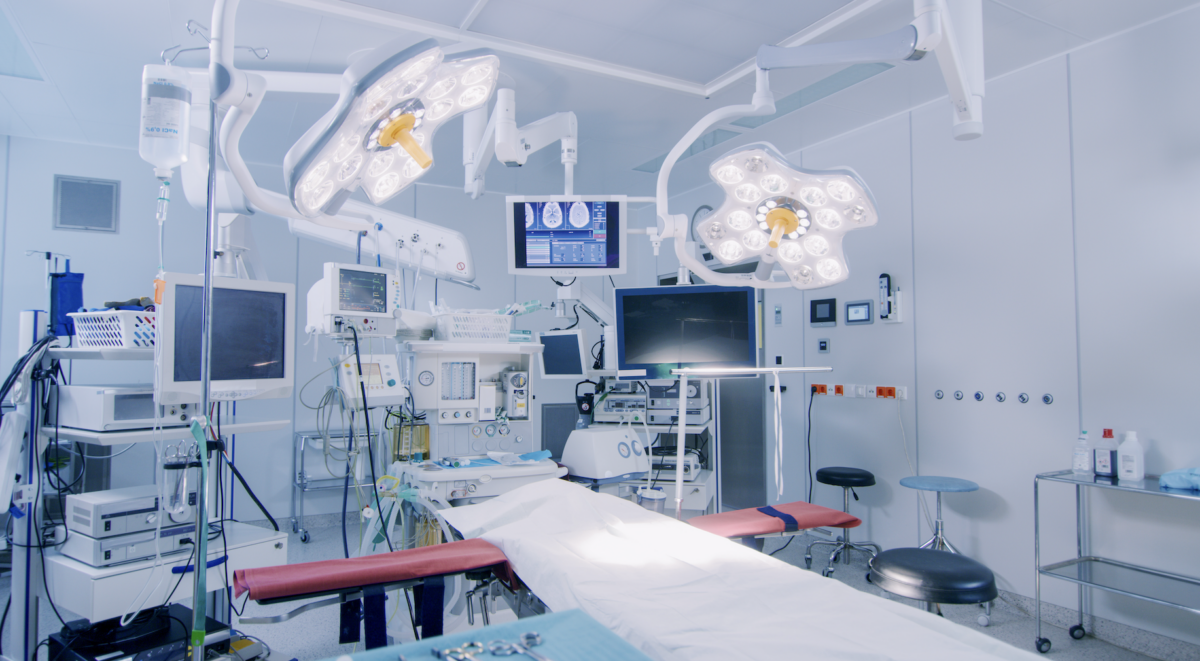
Capabilities in Medical Injection Molding for Illinois Healthcare Manufacturers
We offer a full range of capabilities to meet the diverse needs of Illinois healthcare manufacturers. Whether it’s creating custom tooling or offering precision molding services, JDI Plastics has the resources to produce high-quality medical components at scale. Our secondary services like assembly and packaging further streamline the production process, making us your one-stop shop for injection molding needs.
Biocompatible Materials | FDA-approved thermoplastics and polymers. |
Sterilization Processes | Ensures safe, sterile components ready for use. |
Precision Molding | High accuracy for intricate medical devices. |
Custom Tooling | Tailored molds for unique product designs. |
Regulatory Compliance | Meets all necessary industry standards. |
Custom Medical Components for Various Illinois Medical Applications
At JDI Plastics, we create solutions tailored to the unique needs of the medical industry.
We specialize in delivering products like surgical instruments and diagnostic devices that meet strict healthcare regulations and performance requirements.
Our medical injection molding capabilities can optimize your supply of both single-use devices and long-term medical apparatus – all provided with the highest degree of professionalism, timely service, and customer support.
Illinois medical companies can rely on us for:
- Syringes and other drug delivery systems.
- IV components designed for safe and reliable use.
- Prosthetics crafted with precision and care.
- Diagnostic tools that meet strict healthcare standards.
- Custom disposable elements for various medical applications.
Expertise in FDA-Approved Medical Grade Materials for Injection Molding
Medical injection molding is a strictly regulated service and should always be approached with a clear understanding of every regulation involved – choosing the right materials is essential.
At JDI Plastics, we specialize in working with FDA-approved thermoplastics and biocompatible polymers.
These materials are ideal for creating safe, reliable, and compliant medical devices that meet stringent industry standards. Our products boast long-lasting durability and ensure patient safety.
We understand how important the right material is for every application. Here’s a breakdown of the key types of materials we use and their specific medical applications:
- Thermoplastics: Ideal for surgical instruments and medical device housings due to their rigidity, resistance to sterilization processes, and ability to withstand high temperatures. They are durable, lightweight, and cost-effective for mass production.
- Thermoplastic Elastomers (TPE): Perfect for creating flexible, durable seals and gaskets used in fluid management systems, catheters, and valves. TPEs offer flexibility, chemical resistance, and long-term durability, making them essential for devices that require tight seals and elasticity.
- Biocompatible plastics: Safe for use in devices that come into direct contact with patients, such as prosthetics, implants, and diagnostic devices. These materials are specifically designed to be non-toxic and non-reactive, ensuring patient safety in applications where biocompatibility is critical.
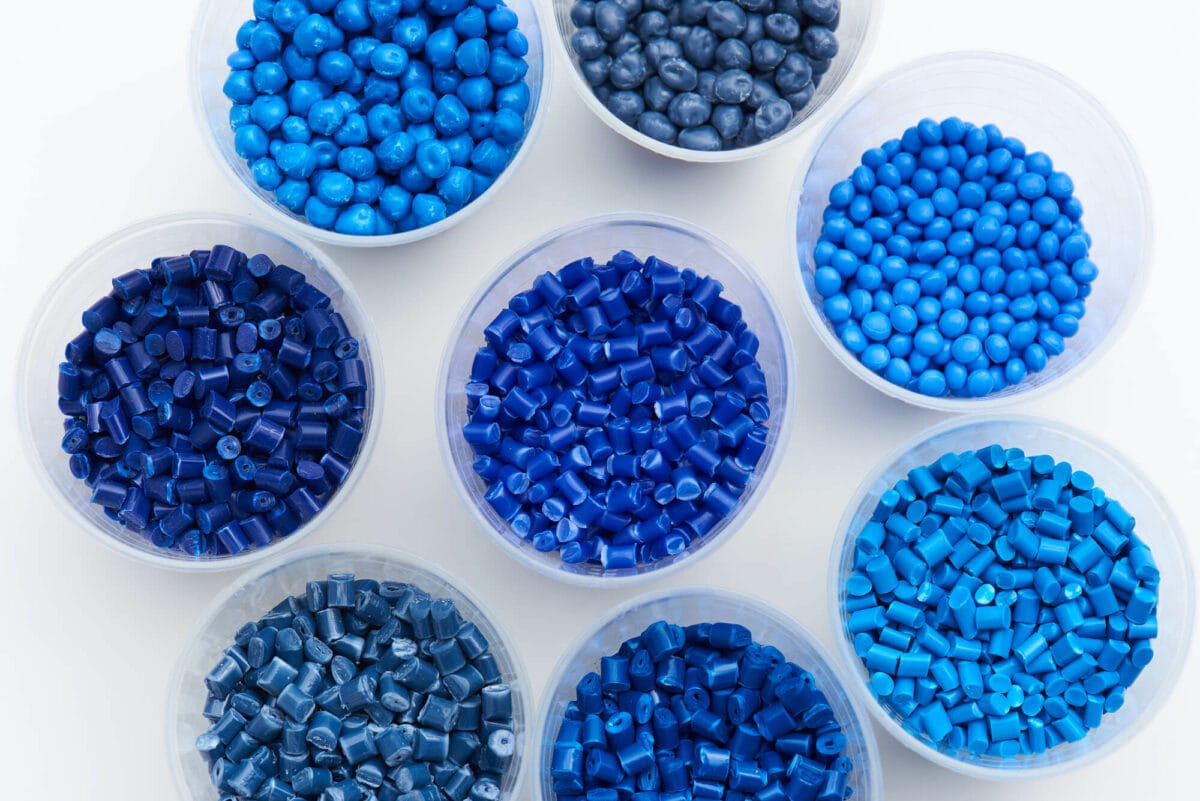
Common Medical-Grade Materials We Mold
JDI Plastics is highly experienced with a wide variety of materials to meet any and all needs:
- Nylon: Known for its strength and durability, ideal for surgical tools and medical device components.
- Polycarbonate: Transparent and impact-resistant, perfect for housings and diagnostic equipment.
- ABS: Offers excellent toughness and heat resistance, used in medical device enclosures.
- Styrene: Lightweight and versatile, often used for disposable medical products.
- TPE (Thermoplastic Elastomer): Provides flexibility, making it suitable for seals, gaskets, and overmolding soft-touch applications.
- HDPE & LDPE: Known for chemical resistance, used in bottles, tubes, and containers for medical liquids.
- PVC (Rigid and Flexible): Used in tubing and medical devices that require flexibility and durability.
- Acetal: Provides high stiffness and low friction, ideal for precision components like gears and clips.
- Polypropylene: Often used for its chemical resistance, recyclability, and biocompatibility, polypropylene is also typically less expensive than alternative materials.
- PEEK: High-performance polymer with excellent chemical and heat resistance, used in implants and medical devices.
- Polysulfone: Sterilization-resistant, suitable for medical applications that require high strength and temperature tolerance.
- PET: Commonly used for transparent medical containers and diagnostic applications.
- Acrylic: Provides clarity and toughness, often used in medical displays and housings.
Frequently Asked Questions About Medical Injection Molding in Illinois
What is medical injection molding?
Medical injection molding is the process of manufacturing high-precision medical components using specialized molds and materials. It’s widely used in the healthcare industry to produce critical devices like syringes, surgical tools, and diagnostic equipment. In Illinois, many medical manufacturers depend on injection molding to create products that meet both FDA and ISO standards for safety and performance.
What is the market for medical injection molding?
The demand for medical injection molding continues to grow in Illinois as the state’s healthcare industry expands. Illinois is home to several leading medical device manufacturers, making the state a hub for high-volume, high-quality medical component production. Injection molding provides the cost-effective, scalable solutions these companies rely on.
What is the lifespan of an injection mold?
The lifespan of an injection mold depends on its design, material, and usage. Molds built with high-quality materials and designed with foresight, like the ones we use at JDI Plastics, can last millions of production cycles. This means long-lasting, high-volume production for Illinois-based manufacturers, reducing the need for frequent mold replacements and keeping production costs down.
JDI Plastics is Your Go-To Medical Injection Molding Partner in Illinois
JDI Plastics is a trusted partner in the medical injection molding industry. Our team is committed to precision, quality, and ISO compliance – and we always provide products that meet the exact needs of our Illinois-based and out of state clients.
From custom solutions to meeting tight production deadlines, we provide the expertise and reliability manufacturers demand.
When it comes to producing high-quality, cost-effective medical components, JDI Plastics has you covered. With our FDA-approved materials, extensive experience, and dedication to customer service, you can count on us to deliver the products you need—when you need them.
Learn more about working with JDI Plastics by visiting our Homepage.
Reach out with questions today!
Markets Served
We tailor our services and requirements around the needs of each individual customer, which allows us to provide the best performance at a very competitive price. We are proud to be able to offer our customers more solutions so that they can narrow down their supply chain and supplier base.