Injection Molding for Tool Manufacturers - Illinois-Based High-Performance Components
Why Injection Molding is Essential for Tool Manufacturers in Illinois
JDI Plastics is an Illinois-based injection molding company trusted by tool manufacturers, offering durable, high-quality components designed to meet the exacting needs of the industry. We keep supply lines running efficiently for in and out of state tool manufacturers.
Plastic injection molding is a cornerstone of modern tool manufacturing because it delivers precision, durability, and cost-efficiency.
Tool manufacturers rely on this process to produce intricate and robust parts that stand up to heavy use. By allowing for high-volume production with minimal waste, injection molding helps manufacturers achieve the precision required for high-performance tools while keeping costs low.
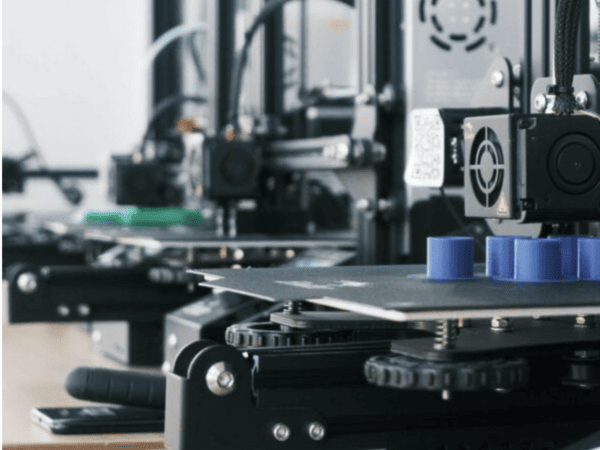
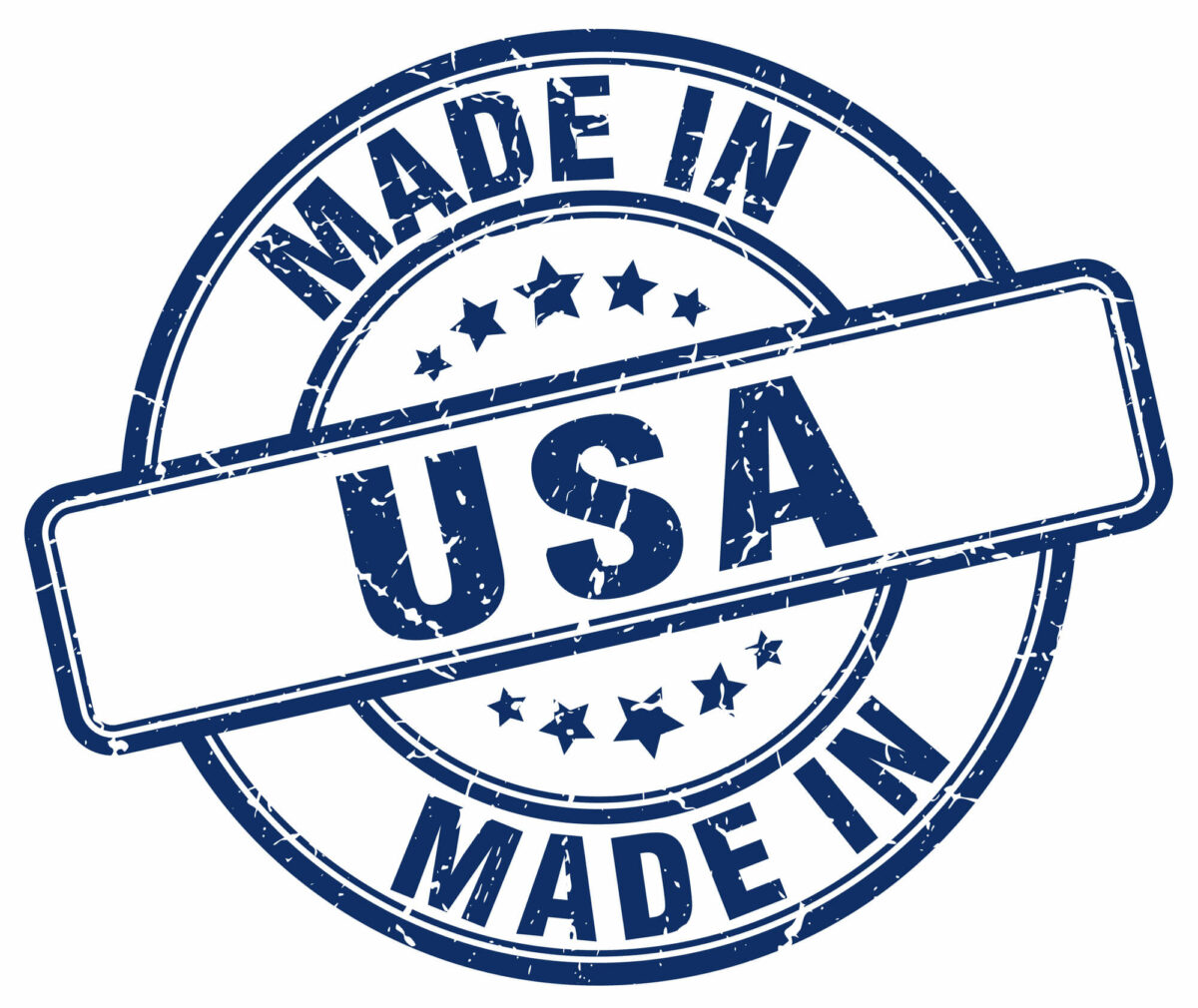
The JDI Advantage
Material strength for withstanding wear and tear.
Design flexibility for creating complex tool components.
Scalability for high-volume production.
High-tolerance production for tight specifications.
Efficiency in reducing material waste and production time.
High-Volume Production | Supports efficient mass production of components, reducing lead times and lowering production costs. |
Precision and Accuracy | Delivers consistent, high-tolerance parts crucial for tools requiring exact dimensions and fit. |
Design Flexibility | Enables customization for ergonomic designs, allowing manufacturers to create comfortable, durable tool grips. |
Durable Materials | Utilizes strong materials like Nylon, ABS, and Polycarbonate, ideal for heavy-duty, high-wear tools. |
Cost-Efficiency | Reduces material waste and streamlines production, optimizing costs for large-scale manufacturing. |
Scalability | Easily scalable for small to large production runs, adapting to varying demands in the tool manufacturing sector. |
Consistent Quality | Ensures every part produced maintains the same quality, vital for maintaining product reliability. |
Complex Designs | Capable of producing intricate internal parts, such as gears and brackets, to meet functional needs. |
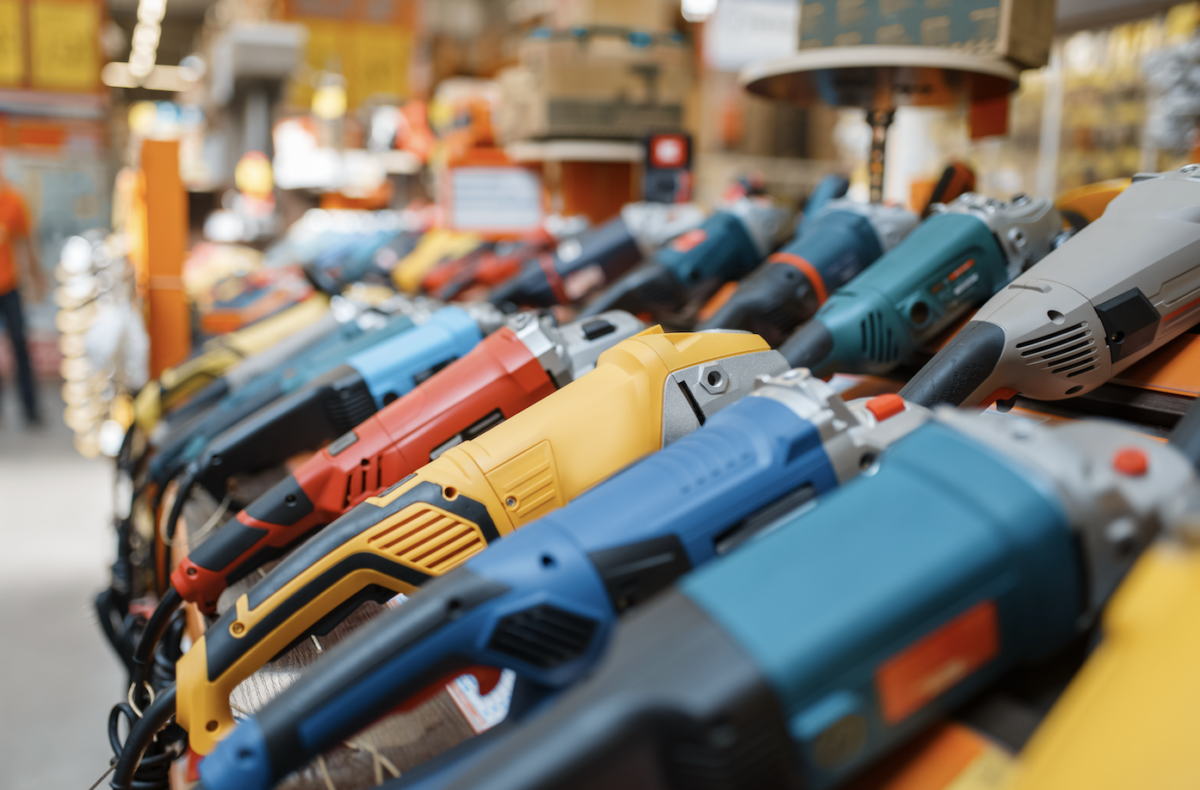
Key Tool Components Produced Through Injection Molding
Injection molding is an essential method for producing many key components used in tools. It allows manufacturers to create durable and ergonomic parts with complex designs, all while maintaining consistent quality.
Components such as handles, casings, and internal mechanical parts benefit from the precision and flexibility injection molding offers.
Tool manufacturers commonly use injection molding to create parts that require both strength and comfort, such as grips and protective housings.
Additionally, the process is ideal for producing internal gears and brackets, which need to meet exact tolerances for proper function.
Examples of Components:
- Tool grips: Ergonomically designed for comfort and durability in hand tools.
- Protective housings: Shields internal mechanisms from external damage in power tools.
- Precision gears: Ensures smooth, reliable operation in mechanical tools.
- Brackets: Provides structural support for various tool components.
- Handles: Custom-shaped, non-slip handles for easy grip and prolonged use.
- Levers and Switches: Durable, precise levers for reliable tool operation.
- Casings: Protective shells for electric or pneumatic tools, offering impact resistance and durability.
Materials Used in Injection Molding for Tools
Tool components require materials that can withstand impact, pressure, and prolonged use.
Injection molding supports a wide range of materials that are ideal for the strength, flexibility, and durability that tool manufacturers need. Each material is selected based on the specific demands of the tool, such as load-bearing capacity or exposure to harsh conditions.
Common Materials:
- Nylon: Strong and resistant to wear, ideal for moving parts.
- ABS: Impact-resistant and durable, used for casings and handles.
- Polycarbonate: Tough and heat-resistant, great for high-stress applications.
- Fiberglass-reinforced plastics: Added strength for components that experience heavy loads or strain.
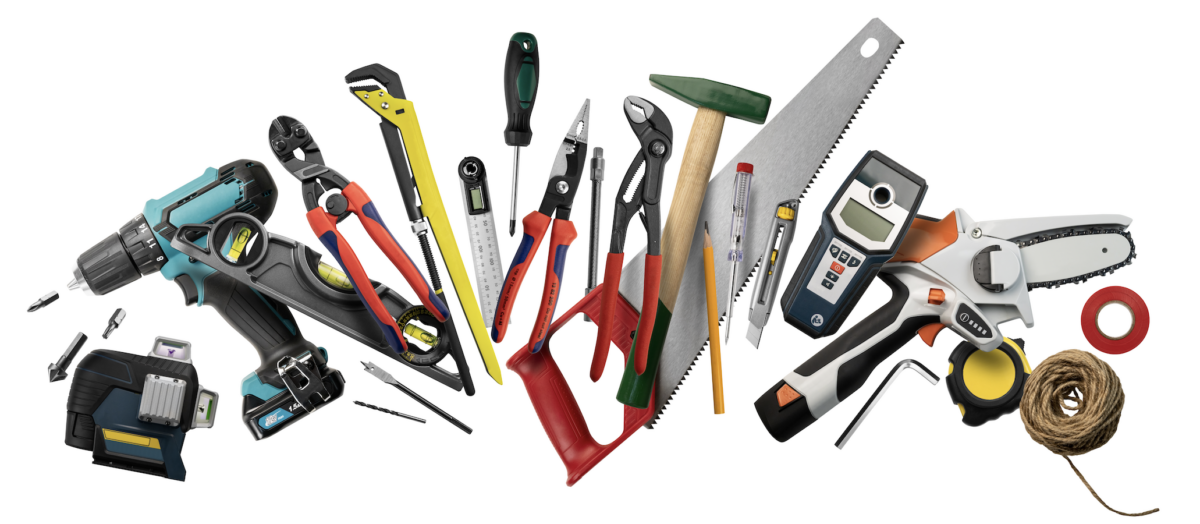
Benefits of Injection Molding for Tool Manufacturers
Injection molding offers several key advantages for tool manufacturers, primarily in cost-efficiency, precision, and flexibility.
The ability to mass-produce high-quality parts with exact tolerances makes it ideal for producing components used in heavy-duty tools. Manufacturers can also benefit from faster production cycles that allow for quicker time-to-market.
Advanced injection molding techniques give tool manufacturers the perk of reduced material waste while maintaining consistent product quality, even in large-scale production.
- Consistent quality
- Faster production cycles
- Reduced material waste
- Scalability for high-volume production
- Customizable designs
Frequently Asked Questions About Injection Molding for Tool Manufacturers
How does injection molding improve tool design innovation?
Injection molding allows for greater design flexibility for tool manufacturers to create more ergonomic and durable parts. This method supports complex shapes and can offer both soft and hard plastics within a single component for the ultimate ergonomic feel.
Can injection molding enhance the durability of tool components?
Yes, by using high-strength materials such as fiberglass-reinforced plastics, injection molding produces tool components that can withstand heavy wear and extreme conditions.
What is the role of customization in injection molding for tools?
Injection molding offers extensive customization options in terms of shape, size, and material selection so manufacturers can create tailored solutions for unique tool requirements and specialized applications.
JDI Plastics is Your Ideal Partner for Injection Molding in Illinois Tool Manufacturing
JDI Plastics is committed to producing high-quality, durable components for tool manufacturers nationwide or in our home state of Illinois. Our precision-focused approach ensures every part meets your specifications while keeping production efficient and cost-effective.
With custom solutions, advanced technologies, and the capacity for high-volume production, JDI Plastics is the ideal partner for tool manufacturers looking for reliable, scalable solutions that enhance product quality and streamline production.
Learn more about working with JDI Plastics by visiting our Homepage.
Reach out with questions today!
Markets Served
We tailor our services and requirements around the needs of each individual customer, which allows us to provide the best performance at a very competitive price. We are proud to be able to offer our customers more solutions so that they can narrow down their supply chain and supplier base.