Why Prototype Injection Molding Matters for Product Development
Prototype injection molding revolutionizes design validation and market testing by allowing manufacturers to quickly create functional prototypes that can be tested for performance, manufacturability, and market feedback before full-scale production.
For example, if a company is designing a smartphone accessory, prototype injection molding would allow them to produce a small batch to test its capabilities and gather feedback before moving on to mass production.
This option allows entrepreneurs, start-ups, and large corporations to refine and improve their products before investing in the final steps to bring them to market.
JDI Plastics is a dedicated resource for high-quality prototype injection molding services. With 29 years of experience, early supplier involvement, and top-quality polymers, JDI stands out as a trustworthy and reliable plastic injection molding company for all industries.
Key Takeaways:
- Accelerates the product development process.
- Enables cost-effective design validation.
- Allows testing of multiple design iterations.
- Provides an avenue for early market testing and consumer feedback.
- Reduces risks associated with large-scale production.
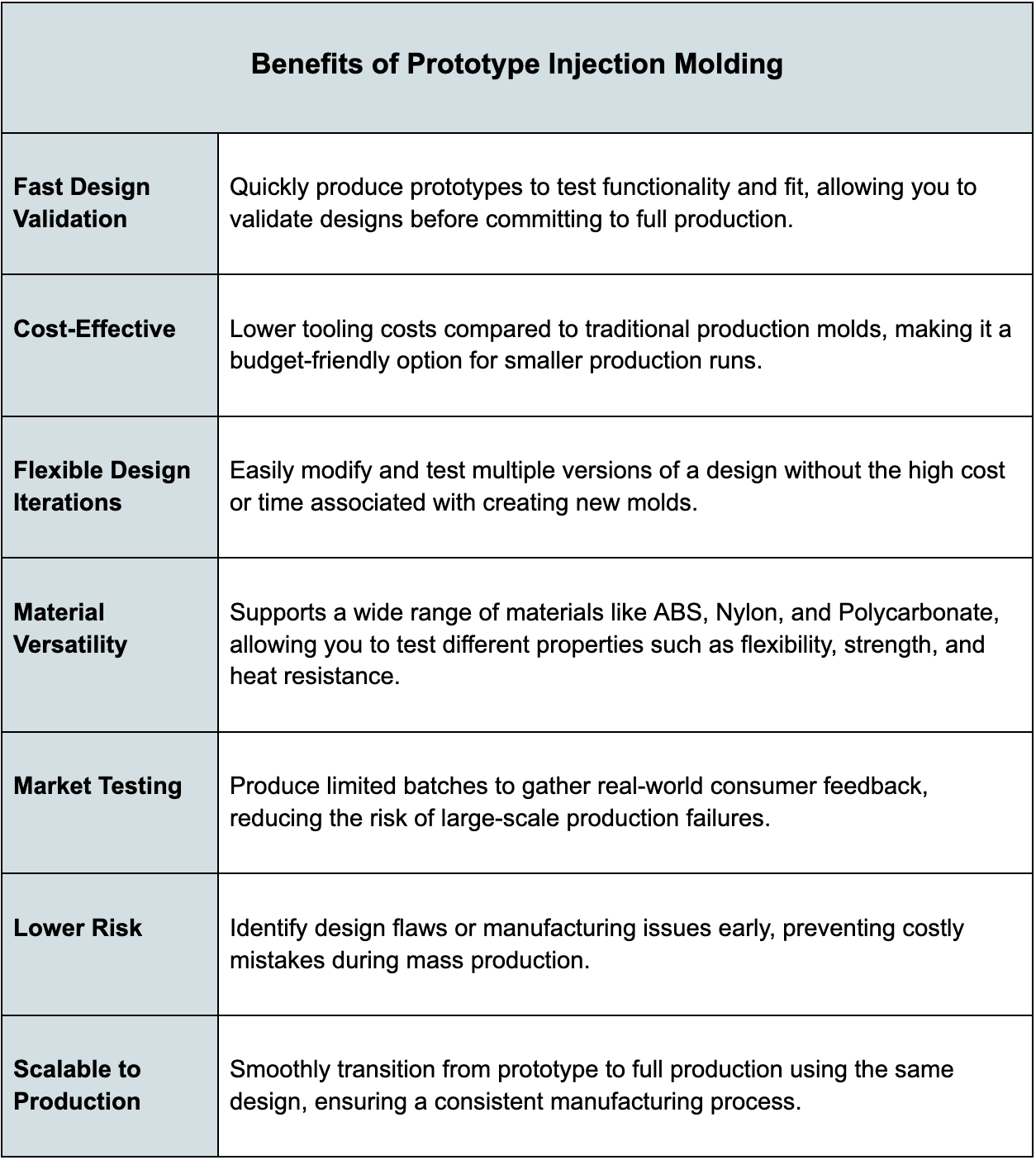
What Is Prototype Injection Molding?
Prototype injection molding is the process of creating functional, small-batch prototypes using injection molding techniques.
It’s primarily used to test and validate designs before mass production. It is an efficient way to ensure the final product meets functional and aesthetic standards.
Think of it as the bridge between concept and reality.
Process Overview:
Here’s how it works:
- Design Creation: A 3D model of the product is developed, serving as the blueprint for the mold.
- Mold Fabrication: A prototype mold is crafted, typically using aluminum, P20 steel or other softer materials for faster turnaround.
- Material Selection: Plastics are chosen based on the product’s requirements—durability, flexibility, or heat resistance.
- Injection Process: Molten plastic is injected into the mold, forming the prototype.
- Testing and Feedback: The finished piece undergoes scrutiny to refine the design and prepare for full-scale production. (1)
Benefits of Prototype Injection Molding
Prototype injection molding brings tangible advantages to product development. It’s fast, cost-effective, and versatile.
- Accelerated Development Timelines: Quickly produce functional prototypes to speed up the R&D phase.
- Lower Tooling Costs: Use cost-effective materials for molds that still deliver precise results.
- Functional Design Validation: Test how well a product works before committing to expensive production molds.
- Market Feedback Opportunities: Small-batch production allows companies to gauge customer reactions before launching full-scale manufacturing.
Applications of Prototype Injection Molding in Design Validation
Prototype injection molding plays a direct role in confirming whether a product is ready for full-scale manufacturing.
Producing functional prototypes allows teams to verify how well a design works in real-world conditions. Functionality, manufacturability, and overall design performance are assessed early, which avoids costly changes down the road.
The process highlights potential flaws that may not surface during digital modeling or 3D printing.
Material testing and stress analysis are critical parts of this phase. Engineers can determine which options offer the best durability, flexibility, or other required properties (such as fire-resistant plastic) by experimenting with various materials and subjecting prototypes to rigorous stress tests.
Applications of Prototype Injection Molding in Market Testing
Small production runs using prototype injection molding give businesses a valuable opportunity to test products in the market.
By producing limited quantities, companies can gather feedback from real customers before scaling up. This approach provides data on usability, design appeal, and demand, helping refine the product while minimizing risk.
Comparing Market-Testing Methods
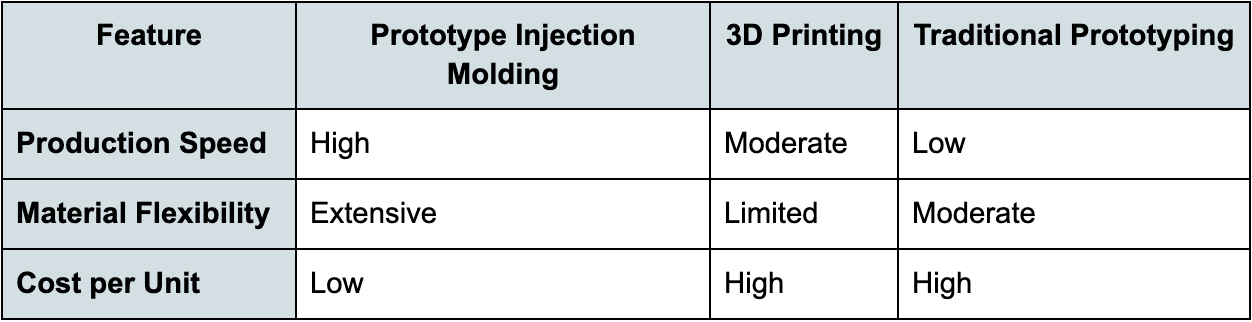
Choosing the Right Material for Prototyping
Material selection is one of the most critical decisions in prototype injection molding.
The material directly impacts the prototype’s performance and determines its suitability for the final product. Choosing the right plastic can mean the difference between a successful prototype and one that needs multiple revisions.
Common materials used in prototype injection molding include:
- ABS: Durable and easy to mold.
- Nylon: Excellent for high-strength applications.
- Polycarbonate: Offers transparency and impact resistance.
- TPE: Provides flexibility for softer parts.
- HDPE: Lightweight and resistant to chemicals.
The Prototype Injection Molding Process in Detail
Designing the Prototype Mold
The mold is the foundation of the entire process. Engineers start by creating a 3D model, which is used to design a prototype mold. These molds are often made from aluminum or other soft metals to reduce costs and speed up production.
Injection and Cooling Phase
Once the mold is ready, molten plastic is injected into the cavity under pressure. The plastic fills the mold to take on the desired shape.
Now the cooling phase begins. The material solidifies and takes on the precise dimensions and features of the mold.
Post-Processing and Inspection
Post-processing ensures a dimensional and functional result after the prototype is ejected from the mold.
This includes trimming excess material, smoothing edges, and conducting detailed inspections. Each piece is checked for accuracy, strength, and alignment with design specifications.
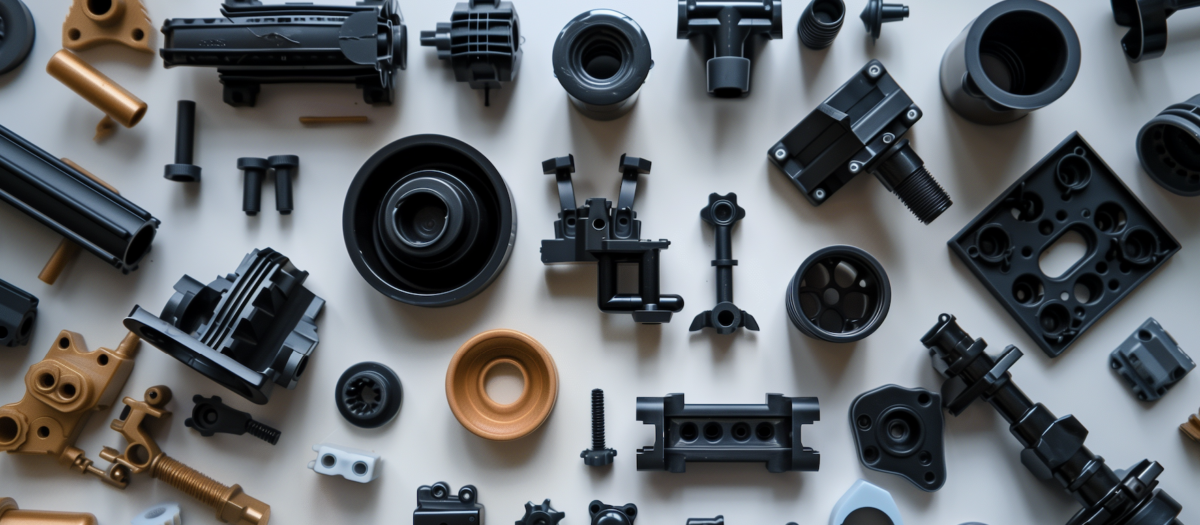
Frequently Asked Questions About Prototype Injection Molding
What is prototype injection molding?
Prototype injection molding is a manufacturing process that uses injection molding techniques to create small-batch prototypes. These prototypes are used to test designs, materials, and functionality before mass production.
Is injection molding a good career?
Yes, injection molding offers a rewarding career with engineering, production, and quality assurance opportunities. It’s vital to many industries, including plastic automotive component design, medical devices, and consumer goods.
Is injection molding rapid prototyping?
Yes, prototype injection molding is a form of rapid prototyping. It’s beneficial for producing functional prototypes that closely resemble the final product.
What are the 5 steps of injection molding?
- Clamping: The mold is securely closed.
- Injection: Molten plastic is injected into the mold.
- Cooling/Plasticizing: The material solidifies into the desired shape and the machine’s screw rotates to feed more material.
- Opening: The mold is opened to release the part.
- Ejection: The finished prototype is removed for inspection.
Conclusion: Revolutionizing Product Development with Prototype Injection Molding
Prototype injection molding transforms how businesses approach product development. It offers fast, accurate, and cost-effective ways to validate designs and test market readiness. With this method, teams can refine their products before committing to large-scale production.
Ready to elevate your prototyping process?
JDI Plastics delivers custom injection molding solutions tailored to your design and market testing needs. Contact us today to start turning your ideas into reality.
Reference:
(1) Efficient Prototyping, Western Carolina University, https://www.wcu.edu/pmi/1993/93PMI365.PDF